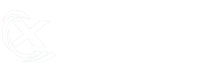
Preparation and process analysis of molybdenum alloy materials such as molybdenum plate, molybdenum wire and molybdenum bar
The brand manufacturer of tungsten and molybdenum materials, Jiritong, shares the performance of the following molybdenum diversion tube, molybdenum hook and other molybdenum materials according to the actual application of the products.
Molybdenum and molybdenum alloy materials, such as molybdenum plate, molybdenum rod, molybdenum wire, molybdenum tube, molybdenum foil, etc. are prepared by powder metallurgy and subsequent deformation processing technology.
11. JPG
The mixed molybdenum and molybdenum alloy powder were prepared by conventional pressing or isostatic pressing. The billet was sintered at high temperature of 2000-2200°C in hydrogen atmosphere to improve its strength and density so that it could adapt to further deformation processing. The sintered billet is extruded, forged, rolled or rolled at a temperature of 1200 ~ 1500°C. The material density increases with the increase of deformation. Forgings, round rods and plates are produced by this process. The coarse wire was prepared by high temperature rolling and drawing, while the fine wire was prepared by low temperature drawing. The melting point of pure molybdenum is up to 2620°C. The high melting point and high temperature strength make the material suitable for use at 1900°C. Molybdenum may recrystallize between 800°C and 1200°C, depending on the surface shrinkage during processing. Spontaneous grain growth occurs from 1600°C to 1800°C, resulting in significant decreases in strength and hardness. Molybdenum, Molybdenum alloy and Molybdenum processing parts have been widely used because of their good high-temperature mechanical stability. Typical applications include:
22. The JPG
1. Lighting industry: Molybdenum pole, molybdenum pin, molybdenum hook and molybdenum ring supporting tungsten filament in traditional incandescent lamps; Tungsten skein core rod; Molybdenum strip sealed with quartz glass in low and high pressure mercury lamps and halogen lamps; A hood used to reduce the brightness of car headlights; High temperature molybdenum wire used for headlamp support rod of automobile and motorcycle.
2. Vacuum tube industry: molybdenum wire used for vacuum closed connection with borosilicate glass in vacuum tube, especially molybdenum pins with polished surface; A grating made of molybdenum wire that can withstand great thermal stress; Gold-plated molybdenum wire for improving electron emission properties; Anodes, auxiliary anodes, cathodic support elements and other structural parts in electron tubes such as transmitting tubes, short-wave tetrode and high-power tetrode; Molybdenum cap and molybdenum pin in microwave magnetron.
3. Semiconductor technology: the thermal expansion coefficient of molybdenum is similar to that of silicon. Molybdenum is widely used in transistors and semiconductor components. High quality molybdenum circular plates for silicon single crystal substrate, molybdenum circular plates and rings for cathodic side connection.
4. Switches and contacts: special contacts for mercury switches and telephone relays.
23. The JPG
5. Isothermal forging: Isothermal forging molds of molybdenum or TZM of titanium alloy and super alloy with high mechanical stability within the temperature range of 900-1100°C.
6. Nuclear technology: sintering device, sintering boat and sintering pan used in nuclear fuel manufacturing, high-temperature flow element used in outer wall protection and reversing module in nuclear fission device.
7. Lighting industry: arc starting electrode of discharge tube, filament, annealed tungsten filament, evaporation boat, welding electrode, etc.
8. Electronics industry: semiconductor substrate, tube gate, anode, passive cooling device radiator, capacitor sintering boat and cup, etc.
9. Medical system: X-ray targets and their fasteners, fixed anodes, detector components, collimators, shielding covers, containers and accessories.
10, high temperature furnace manufacturing: heating body, heat insulation screen, material rack and other components, sintering boat, fastener, etc.